
Introduction: The High Stakes of Seal Failures in Oil and Gas
Imagine an offshore oil rig in the Arabian Sea, waves crashing, drills roaring. It’s 2 a.m., and engineer Arjun gets a call: a pump seal has failed. Crude oil seeps, equipment stalls, and every minute costs thousands. Downtime isn’t just inconvenient—it’s a financial hemorrhage. Safety risks climb, and regulators loom. For Arjun, who shared his story at an industry expo, this was a wake-up call about mechanical seals for oil and gas.
Seal failures in oil and gas aren’t rare—they’re a persistent threat. High pressures, abrasive fluids, and scorching temperatures push seals to their limits. At Orbit Fluid Solution LLP, we’ve spent over three decades designing high-pressure sealing solutions to keep rigs like Arjun’s running. In this guide, we’ll unpack what causes seal leaks in oil rigs, why high-pressure seals are critical, and how to extend seal life with practical, proven strategies. Whether you’re on a rig or a refinery, this guide will equip you to prevent seal failure oil rigs and beyond. Let’s get started.
Why Seal Failures Are a Big Deal in Oil and Gas
Oil and gas operations are unforgiving. A single seal failure can:
- Halt Production: Downtime costs can hit $100,000/hour on rigs, per industry reports.
- Risk Safety: Leaks spark fires or toxic exposure—think Deepwater Horizon’s lessons.
- Hurt the Bottom Line: Cleanup, repairs, and fines pile up fast.
Arjun’s rig lost a week last year to a failed seal. The fix? Expensive. The lesson? Preventing seal failures in oil and gas saves more than just time—it saves careers and companies.
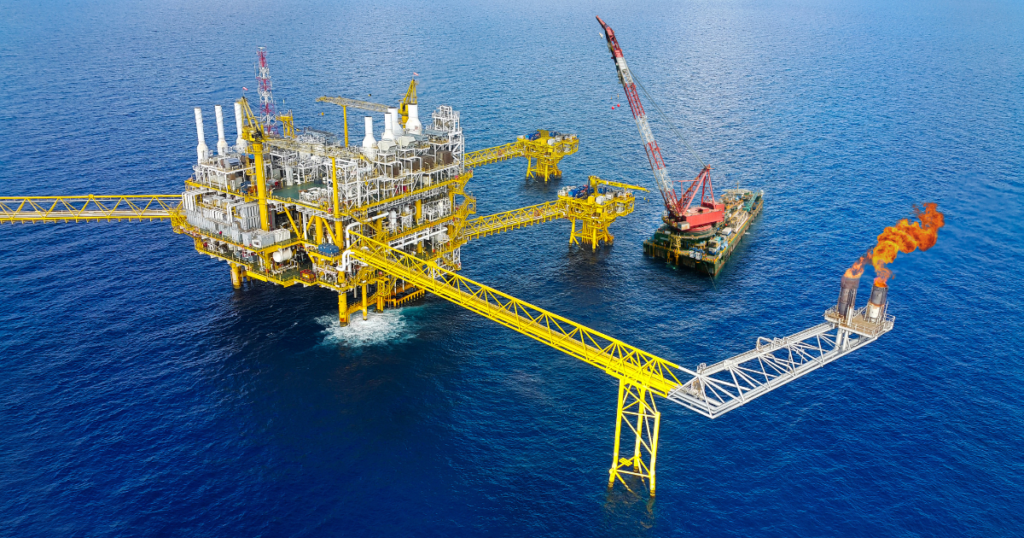
Understanding Seal Failures: What Goes Wrong?
To prevent failures, we must first know why they happen. Mechanical seals for oil and gas face brutal conditions. Here are the top culprits, with failure analysis:
1. High Pressure Overload
- What: Pressures exceeding 10,000 psi crush standard seals, deforming faces.
- Why Costly: Leaks disrupt drilling, risking blowouts.
- Failure Rate: ~30% of rig seal failures, per SPE Journal.
2. Abrasion from Slurries
- What: Sand and drilling mud grind seal faces, eroding them.
- Why Costly: Abrasive wear shortens seal life to weeks.
- Failure Rate: Common in shale gas, ~25% of cases.
3. Thermal Stress
- What: Temperatures above 200°C warp materials like rubber.
- Why Costly: Heat-induced cracks cause sudden leaks.
- Failure Rate: ~20% in refineries, per industry audits
4. Chemical Attack
- What: Corrosive fluids (e.g., H2S) degrade elastomers.
- Why Costly: Seal breakdown contaminates systems.
- Failure Rate: ~15% in sour gas fields.
5. Installation Errors
- What: Misalignment or overtightening cracks seals.
- Why Costly: Early failures waste time and parts.
- Failure Rate: ~10%, often human error.

The Cost of Failure: A Closer Look
Why care? Because the ripple effects are massive:
- Financial: A North Sea rig lost $2M in 2023 to a seal-related shutdown (Oil & Gas Journal).
- Environmental: Leaks pollute oceans, drawing fines and PR disasters.
- Operational: Delayed projects erode client trust.
Arjun’s team faced a $500,000 hit from one incident. High-pressure seals aren’t just parts—they’re your operation’s lifeline.
How Orbit’s Seals Prevent Failures
At Orbit Fluid Solution LLP, we don’t just react to failures—we stop them. Our mechanical seals for oil and gas are built to thrive under pressure. Here’s how:
- Pressure Resistance: Our double cartridge seals handle 15,000 psi, with hardened faces (tungsten carbide).
- Abrasion Defense: Silicon carbide coatings resist slurry wear, extending life 3x vs. standard seals.
- Thermal Stability: Seals rated to 300°C, using PEEK for extreme heat.
- Chemical Durability: PTFE and Viton elastomers shrug off H2S and acids.
- Error-Proof Design: Pre-assembled cartridge seals reduce installation mistakes.

Step 1: Choose the Right Seal for Your Rig
Selecting seals starts with your conditions:
- Pressure: Deepwater rigs need double seals.
- Fluid Type: Slurries demand abrasion-resistant seals (SPE abrasion study).
- Temperature: Refineries require heat-stable seals.
Arjun’s rig switched to our tungsten carbide cartridge seals—failures plummeted. Map your specs first.
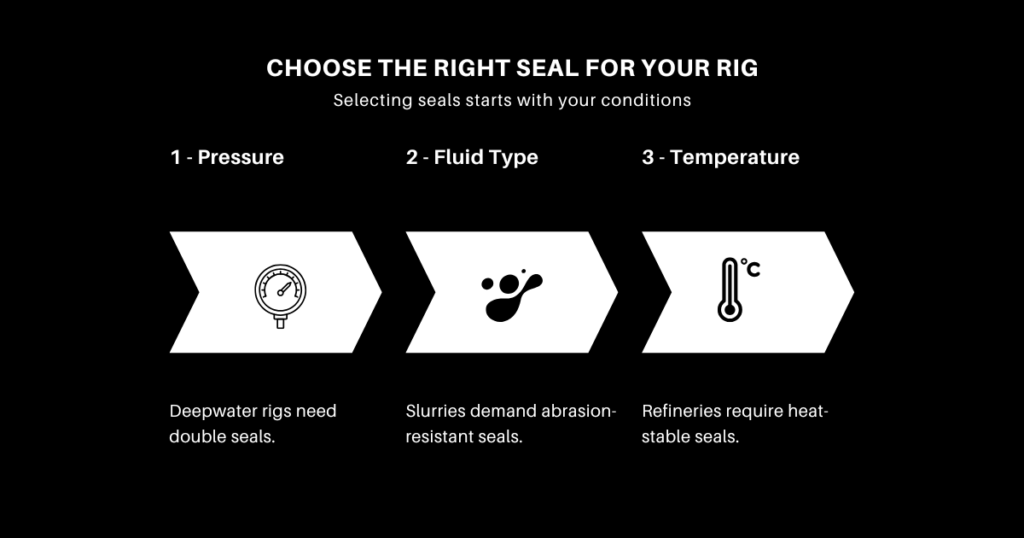
Step 2: Master Installation
A great seal fails if installed poorly. Tips:
- Align Precisely: Use laser alignment tools (±0.01mm).
- Torque Correctly: Follow specs (e.g., 20 Nm for 2” seals).
- Clean Thoroughly: Debris causes instant wear.

Step 3: Build a Maintenance Schedule
Extend seal life with routine care:
- Daily: Check for leaks or vibrations.
- Monthly: Inspect seal faces for wear.
- Quarterly: Flush systems to clear debris.
Arjun’s team now logs checks—seal life doubled.
Case Study: An Offshore Rig Turnaround

Technical Specs: What Makes Our Seals Stand Out
- Pressure Rating: Up to 15,000 psi (API 682 compliant).
- Material Hardness: Tungsten carbide (Hv 1500).
- Temp Range: -40°C to 300°C.
- Leak Rate: <0.1 ml/hr under test conditions.

Common Mistakes to Avoid
- Wrong Seal: Standard seals crack under pressure.
- Skipping Flushes: Mud buildup kills seals.
- Ignoring Wear: Small cracks grow fast.
The Future of Oil and Gas Seals
Smart seals with sensors are emerging—real-time pressure monitoring is next. At Orbit, we’re pioneering sustainable seals with recycled composites. Stay tuned.
Conclusion: Seal Your Operation’s Future
Preventing seal failures in oil and gas isn’t just technical—it’s strategic. From choosing high-pressure sealing solutions to maintaining them, every step counts. At Orbit Fluid Solution LLP, we’re here to ensure your rigs run leak-free. Visit orbitseals.com or contact us—let’s keep your operation flowing.