
Introduction: A Tale of Seals and Safety
Picture this: a bustling food processing plant, humming with machinery—pumps whirring, mixers churning, and pipes flowing with everything from creamy sauces to sugary syrups. It’s a symphony of production, feeding millions daily. But then, a tiny drip forms. A seal fails. Suddenly, contamination risks spike, downtime looms, and regulators knock. For plant managers like Ravi, who I met at a trade show last year, this isn’t just a headache—it’s a nightmare threatening his entire operation.
That’s where mechanical seals for food processing come in. These unsung heroes keep your equipment leak-free, your products safe, and your compliance intact. At Orbit Fluid Solution LLP, we’ve spent over 30 years perfecting these solutions, and today, I’m sharing the ultimate guide to choosing the right food-safe seals for your plant. Whether you’re battling sticky residues or strict hygiene standards, this post will arm you with the knowledge to make informed decisions. Ready to seal the deal on safety and efficiency? Let’s dive in.
Why Mechanical Seals Matter in Food Processing
In the food industry, every component counts. A single leak can spoil a batch, halt production, or—worse—land you in hot water with agencies like the FDA or EHEDG. Ravi’s story isn’t unique. He told me how a worn-out seal once cost his plant a week of downtime and thousands in lost product. The stakes are high, and mechanical seals are your first line of defense.
Here’s why they’re critical:
- Leak Prevention: They stop fluids from escaping pumps and mixers, protecting your product integrity.
- Hygiene Assurance: Food-safe mechanical seals resist contamination, meeting stringent sanitary standards.
- Efficiency Boost: Reliable seals reduce downtime, keeping your lines running smoothly.
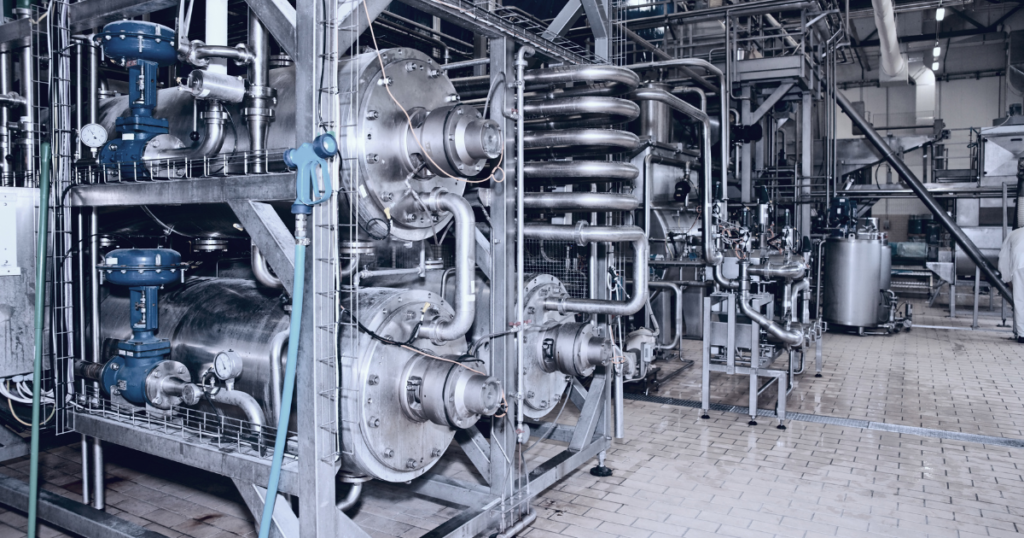
Understanding Mechanical Seals: The Basics
Before choosing, let’s unpack what mechanical seals are. Imagine two precision-engineered faces—one stationary, one rotating—pressed together to form a barrier between your equipment and the outside world. At Orbit, we craft these with materials like stainless steel and FDA-approved elastomers, ensuring they withstand food’s unique challenges—think acidic juices or abrasive spices.
There are several types to know:
- Single Mechanical Seals: Simple, cost-effective, ideal for low-risk fluids like water.
- Double Mechanical Seals: Extra protection with a barrier fluid, perfect for sticky or hazardous mixes.
- Cartridge Seals: Pre-assembled for easy installation, a favorite in fast-paced plants.

-
16 Apr 2025 Seal Failure and PreventionTop 10 Causes of Mechanical Seal Leaks and How to Fix Them
-
16 Apr 2025 Industry-Specific Seal SolutionsHow to Prevent Seal Failures in Oil and Gas Applications: A Comprehensive Guide
-
05 Apr 2025 Industry-Specific Seal SolutionsThe Ultimate Guide to Choosing Mechanical Seals for the Food Processing Industry
The Food Processing Challenge: What Makes It Unique?
Food processing isn’t like other industries. Ravi’s plant handles everything from dairy to sauces, each with distinct demands. Your seals must tackle:
- Sanitation Standards: Hygienic seals for food industry must comply with FDA, 3-A, or EHEDG rules—no crevices for bacteria to hide.
- Temperature Extremes: From freezing dairy lines to boiling syrup vats, seals need thermal resilience.
- Sticky Situations: Viscous fluids like honey or chocolate can clog or degrade lesser seals.
Last month, I visited a client’s facility where a cheap seal failed under hot tomato puree. The cleanup? Brutal. The lesson? Cutting corners costs more. That’s why choosing the right mechanical seals for food safety is non-negotiable.
Step 1: Assess Your Application Needs
Choosing starts with understanding your setup. Ask yourself:
- What’s the Fluid? Milk needs different seals than abrasive spices.
- Pressure Levels? High-pressure pumps demand robust designs like double cartridge seals.
- Temperature Range? Hot processes need heat-resistant materials like silicon carbide.
Ravi’s team learned this the hard way. After switching to our custom seals for their yogurt line, leaks dropped to zero. Map your needs first—it’s the foundation of a smart choice.
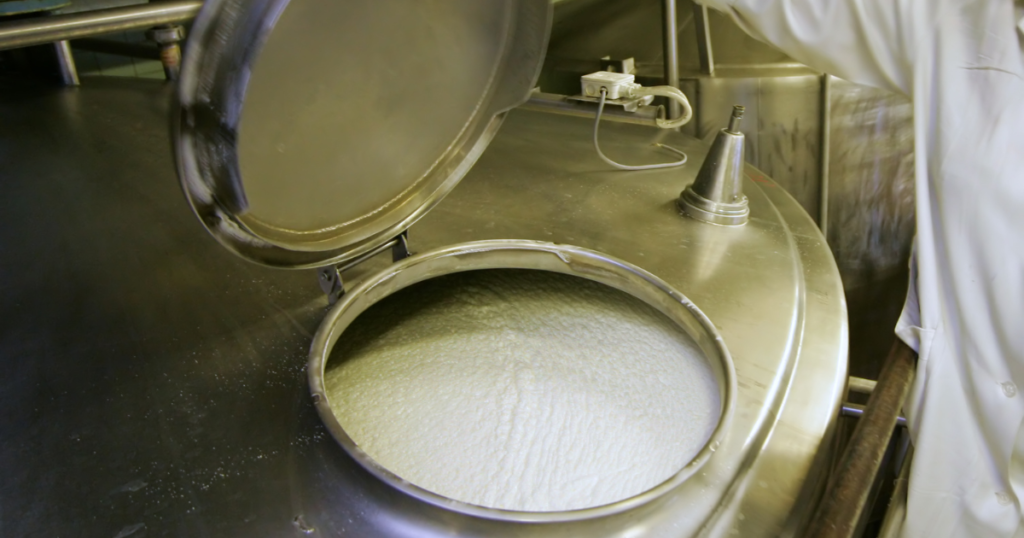
Step 2: Pick the Right Seal Type
Now, let’s match your needs to a seal:
- Single Seals: Great for water or thin liquids.
- Double Seals: Ideal for thick or risky fluids—think sauces or juices.
- Cartridge Seals: Quick to install, perfect for tight maintenance windows.
Pro tip: For high-hygiene needs, opt for sanitary cartridge seals. They’re pre-assembled and polished to eliminate contamination risks.
Step 3: Choose Food-Safe Materials
Materials make or break your seal. At Orbit, we use:
- Stainless Steel: Corrosion-resistant, FDA-approved for food contact.
- Silicon Carbide: Tough against abrasives, heat-stable for hot processes.
- PTFE: Non-stick, chemical-resistant, ideal for sticky fluids.
Avoid cheap rubber seals—they degrade fast and risk leaching. Ravi’s switch to PTFE seals cut his replacement costs by 40%.

Step 4: Prioritize Hygiene and Compliance
Food safety isn’t optional—it’s law. Your seals must:
- Be EHEDG-certified or 3-A compliant for sanitary design.
- Have smooth surfaces—no cracks for bacteria to grow.
- Withstand CIP (Clean-in-Place) chemicals without breaking down.
Our seals at Orbit meet these standards. Link to to verify. Non-compliant seals? They’re a recall waiting to happen.
Step 5: Installation and Maintenance Tips
Even the best seal fails if installed wrong. Here’s how to nail it:
- Align Properly: Misalignment causes leaks—use a laser tool if possible.
- Lubricate: A thin layer of food-grade lube extends seal life.
- Schedule Checks: Monthly inspections catch wear early.
Ravi’s team now uses our installation guide—downtime’s a distant memory.

-
The Ultimate Guide to Choosing Mechanical Seals for the Food Processing Industry05 Apr 2025 Industry-Specific Seal Solutions
-
How to Prevent Seal Failures in Oil and Gas Applications: A Comprehensive Guide16 Apr 2025 Industry-Specific Seal Solutions
-
Top 10 Causes of Mechanical Seal Leaks and How to Fix Them16 Apr 2025 Seal Failure and Prevention
Why Orbit Fluid Solution LLP? Our Edge
Why trust us? Because we’ve lived this industry for decades. Our seals:
- Are custom-engineered for your exact needs.
- Use sustainable materials, cutting waste and emissions.
- Backed by 30+ years of precision craftsmanship.
Ravi’s plant runs smoother today because he chose Orbit. Ready to join him? Explore our complete range of Mechanical Seals designed for Food & Beverage Industry .
Real-World Wins: A Case Study

Common Mistakes to Avoid
Don’t trip over these:
- Cheap Seals: They fail fast—spend once, not twice.
- Ignoring Specs: A seal for juice won’t handle syrup.
- Skipping Maintenance: Neglect kills even the best seals.
Learn from others’ missteps—choose wisely.