
Introduction: The Silent Threat of Seal Leaks
It’s a sweltering day at a Gujarat refinery. Maintenance engineer Sameer notices a drip beneath a pump. A mechanical seal leak—small but sinister. Within hours, the leak escalates, halting production, costing thousands, and risking a safety violation. Sameer’s story, shared over coffee at an industry meetup, isn’t rare. Leaks plague plants worldwide, from food processing to water treatment.
Why do seals leak? What makes them so costly? How can you stop them? At Orbit Fluid Solution LLP, we’ve tackled mechanical seal leaks for over 30 years, and we’re here to share the answers. In this guide, we’ll reveal the top 10 causes of seal leaks, their impact, and proven ways to fix seal leaks—and prevent seal leaks for good. Whether you’re battling drips or planning upgrades, this post is your roadmap to leak-free operations. Let’s dive in.
Why Mechanical Seal Leaks Matter
A tiny leak might seem trivial, but its ripple effects are massive:
- Downtime Costs: A refinery can lose $50,000/hour
- Safety Risks: Leaks spark fires or contaminate food products.
- Regulatory Fines: Violations hit hard—think FDA or EPA penalties.
Sameer’s leak cost his plant $100,000 in repairs and lost output. Understanding why leaks happen is the first step to stopping them.

What Are Mechanical Seals and Why Do They Leak?
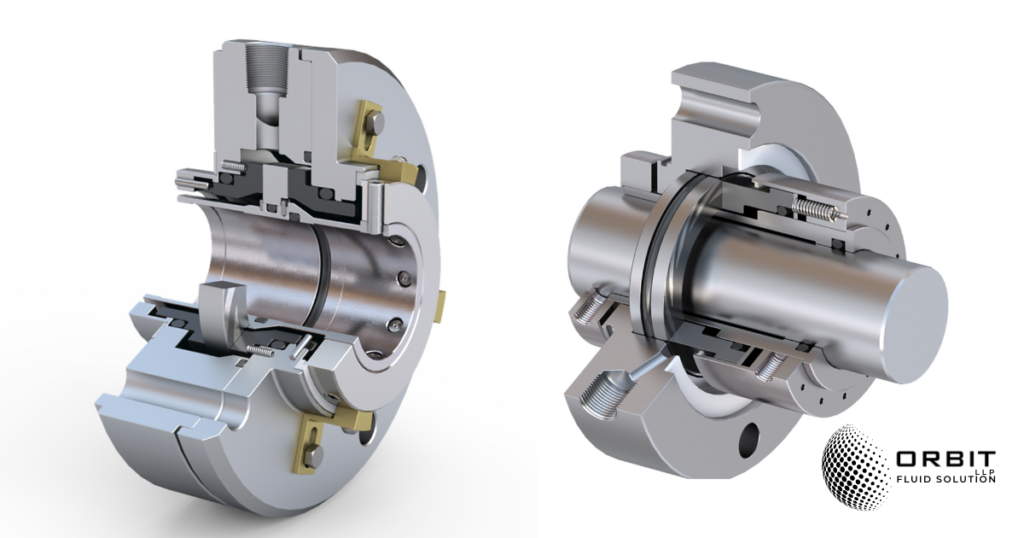
Top 10 Causes of Mechanical Seal Leaks
Here’s the hit list, with fixes for each.
Cause 1: Misalignment
- What: Shaft misalignment skews seal faces, causing uneven wear.
- Impact: Leaks in weeks; ~20% of failures (Pump Engineer).
- Fix: Use laser alignment tools (±0.01mm). Recheck post-install.
Cause 2: High Pressure Overload
- What: Pressures beyond rating (e.g., >5000 psi) crush faces.
- Impact: Sudden leaks, risky in oil rigs.
- Fix: Choose high-pressure seals like Orbit’s tungsten carbide.
Cause 3: Abrasive Wear
- What: Sand or slurries grind faces (silicon carbide resists best).
- Impact: Common in pulp & paper, cuts life by 50%.
- Fix: Use abrasion-resistant seals (SPE abrasion guide).
Cause 4: Thermal Damage
- What: Heat (>200°C) warps elastomers like rubber.
- Impact: Cracks in refineries, food vats.
- Fix: Select PEEK or PTFE seals, rated to 300°C.
Cause 5: Chemical Corrosion
- What: Acids or H2S degrade materials.
- Impact: Leaks in chemical plants, ~15% of cases.
- Fix: Use Viton elastomers.
Cause 6: Dry Running
- What: No fluid lubrication burns faces.
- Impact: Food processing pumps fail fast.
- Fix: Install double seals with barrier fluid.
Cause 7: Improper Installation
- What: Overtightening or dirt cracks seals.
- Impact: Immediate leaks, ~10% of failures.
- Fix: Follow torque specs (e.g., 20 Nm). Clean thoroughly.
Cause 8: Vibration
- What: Machine shakes loosen seals.
- Impact: Water treatment plants suffer most.
- Fix: Balance rotors; use cartridge seals for stability.
Cause 9: Seal Face Contamination
- What: Debris (e.g., pulp) sticks to faces.
- Impact: Leaks in sticky fluids like syrups.
- Fix: Flush systems before startup.
Cause 10: Material Mismatch
- What: Wrong seal for fluid (e.g., rubber in oil).
- Impact: Fast degradation, cross-industry issue.
- Fix: Match seals to specs.
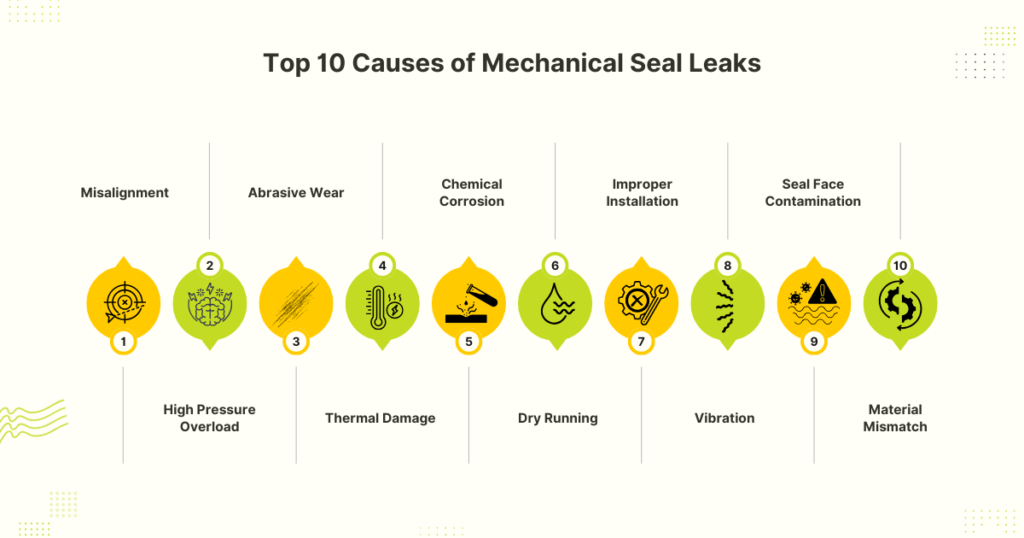
The Cost of Ignoring Leaks
Leaks aren’t just annoying—they’re expensive:
- Financial: A food plant lost $200,000 to a contaminated batch (Food Safety Magazine).
- Environmental: Oil spills draw fines (EPA).
- Reputation: Clients ditch unreliable suppliers.
Sameer’s leak nearly cost his job. Preventing seal leaks is mission-critical.
How to Fix Seal Leaks: A Step-by-Step Approach
When leaks strike, act fast:
- Diagnose: Check for misalignment, wear, or debris.
- Shut Down Safely: Isolate the pump.
- Replace Seal: Use Orbit’s cartridge seals for speed.
- Test Run: Monitor for drips at low speed.
- Log It: Track failures to spot patterns.
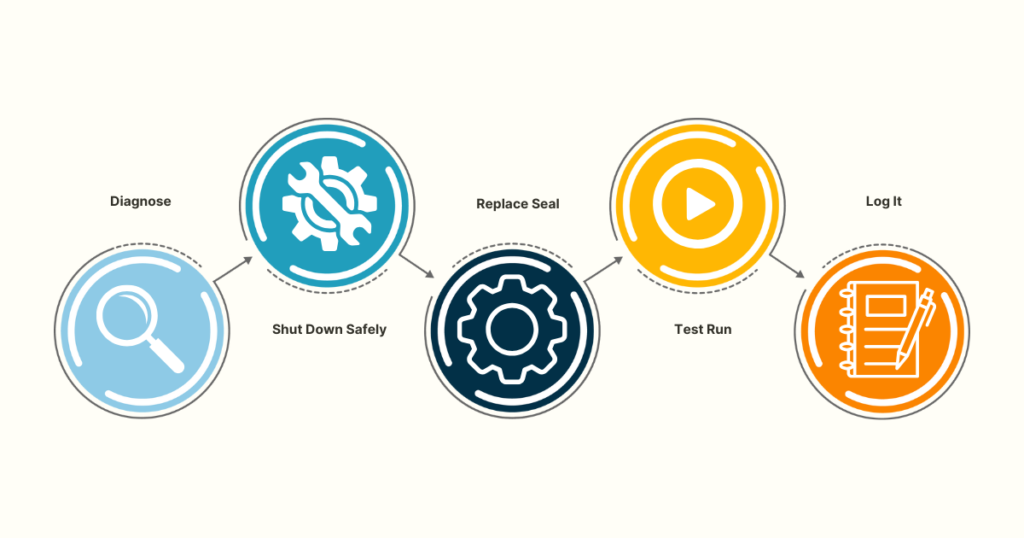
Preventing Leaks Before They Start
Better than fixing? Preventing. Try this:
- Choose Right: Match seals to fluid/pressure.
- Install Smart: Laser-align, torque precisely.
- Maintain Regularly: Monthly checks, annual flushes.
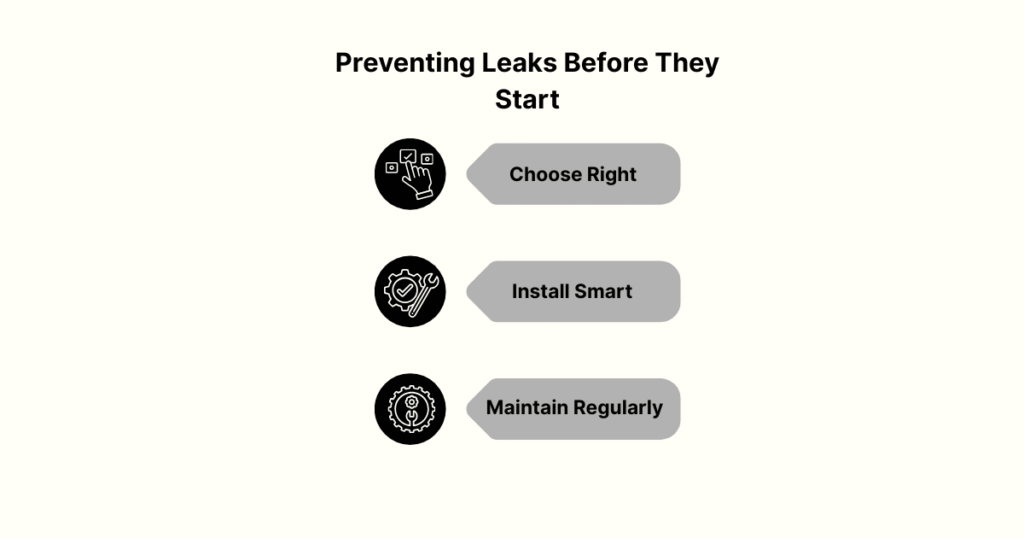
Orbit’s Solutions: Built to Stop Leaks
Our seals tackle leaks head-on:
- Tungsten Carbide: 3x abrasion resistance.
- Double Seals: No dry running risks.
- Custom Fits: From food to oil rigs.
Sameer’s refinery now uses our seals—leaks are history.

Case Study: A Pulp Mill’s Leak-Free Leap
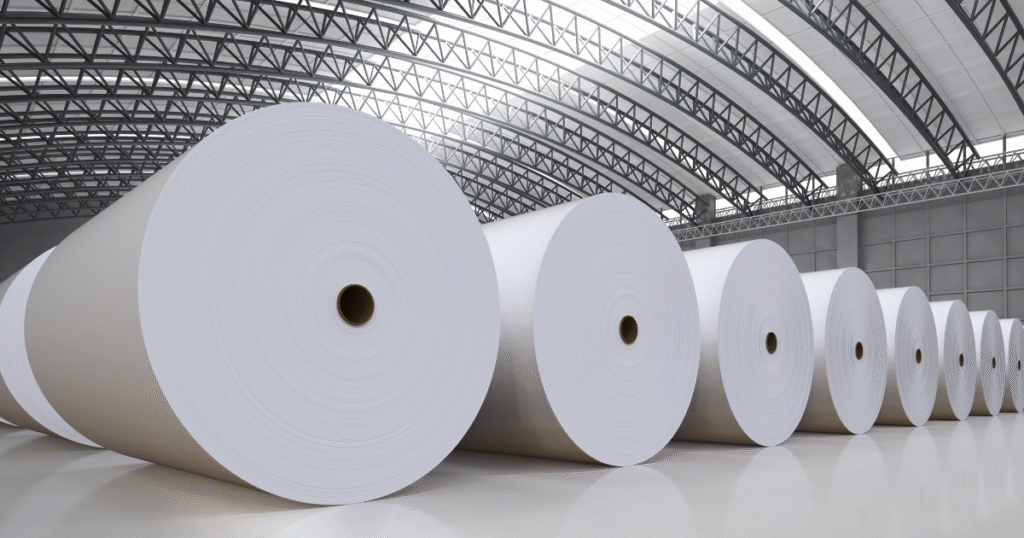
Technical Specs: What Our Seals Offer
- Pressure: Up to 10,000 psi (API 682).
- Temp: -40°C to 300°C.
- Materials: Tungsten carbide, PTFE, Viton.
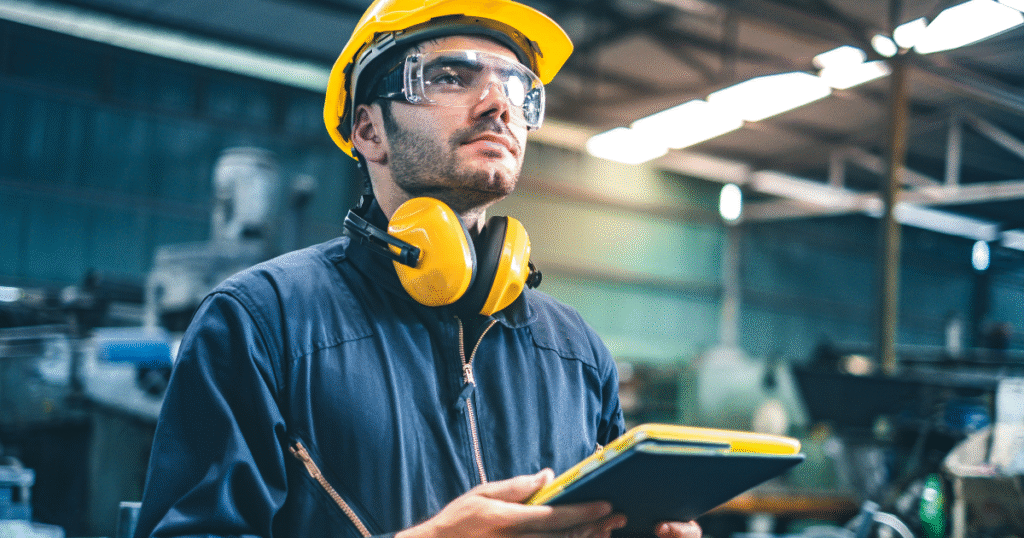
Common Myths About Seal Leaks
- Myth: “All leaks mean bad seals.” Reality: Installation often fails.
- Myth: “Cheap seals save money.” Reality: They cost more in downtime.
The Future of Leak Prevention
Smart seals with sensors are coming—think leak alerts via IoT. Orbit’s testing graphene-based seals for durability. Join us at .
Conclusion: Stop Leaks, Start Winning
Mechanical seal leaks don’t have to derail you. From misalignment to material mismatches, we’ve covered the top 10 causes and how to fix seal leaks. Orbit Fluid Solution LLP is your partner to prevent seal leaks. Visit orbitseals.com or call us—let’s seal your success.